The Quality Standard Paradox: How Rice Grading Creates Wrong Incentives
- "The Grain Guru"
- Mar 27
- 3 min read
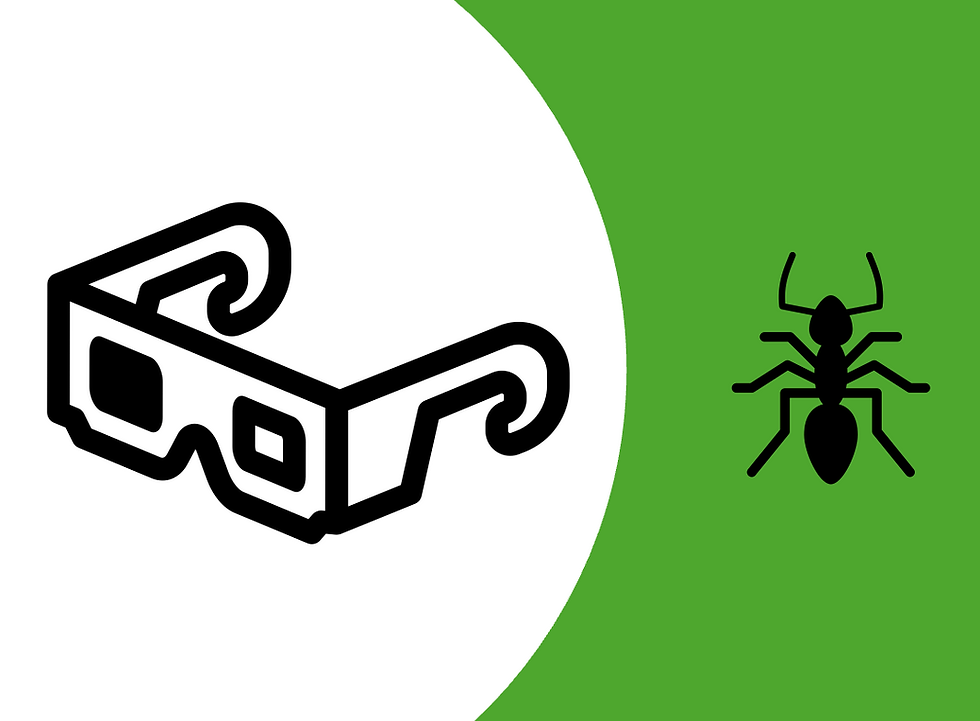
Introduction
International standards ensure quality, consistency, and fair pricing in global rice trading. However, the metrics designed to maintain quality can sometimes incentivize behavior that undermines the standard's original intent. This phenomenon, which I call the "Quality Standard Paradox," is particularly evident in rice grading based on the percentage of broken kernels.
Rice grading systems typically classify kernels into three main classes: whole kernels, head rice (fragments larger than ¾ of average length), and broken rice (fragments smaller than ¾ of average length). International standards for premium commercial rice varieties typically specify a maximum limit of 5% broken kernels, with price penalties for exceeding this threshold.
Understanding Rice Grading Standards
Rice grading is a complex process where multiple factors determine quality and price. Among these factors, the percentage of broken kernels stands out as particularly significant, as broken rice sells for approximately half the price of whole kernels on global markets. Additionally, shipments with more than 5% broken kernels are downgraded, significantly reducing their market value.
According to ISO 7301 and many other international standards, a kernel is classified as "broken" when its length falls below 75% (three-quarters) of the average length of the graded sample. The standard employs detailed measurement protocols using statistical sampling methods to determine this average. This seemingly straightforward definition creates unexpected consequences in practice.
The Paradox Explained
The paradox emerges from how the broken threshold is calculated as a relative measurement rather than based on absolute kernel dimensions. Consider these examples:
• Pure long-grain sample: In a batch of pure long-grain rice with an average kernel length of 7.0mm, the broken threshold would be 5.25mm (75% of 7.0mm).
• Blended sample: If shorter grains are added to reduce the sample's average length to 6.6mm, the broken threshold drops to 4.95mm (75% of 6.6mm).
This 0.3mm difference in threshold (5.25mm vs. 4.95mm) creates a critical "rescue zone." Any kernel fragments between 4.95-5.25mm that would be classified as "broken" in the pure sample can now be classified as "head rice" in the blended sample—despite being physically identical.
This relative definition creates a perverse incentive: suppliers of longer-grain rice can strategically blend in other varieties or shorter grains to reduce the sample's average length, lowering the threshold for a "broken" kernel.
The Economic Motivation
The financial incentive behind this practice is significant. Suppliers can effectively "rescue" kernels that would otherwise be classified as broken by introducing shorter grains into a batch of premium long-grain rice.
To quantify this advantage:
• If 8% of a one-metric-ton shipment consists of "rescued" grains, given a price difference of $500/ton between the whole ($1000/ton) and broken ($500/ton) rice. The additional profit amounts to $40 per ton
When multiplied across large international shipments of thousands of tons, this manipulation can represent hundreds of thousands of dollars in additional revenue per shipment.
This practice, which I term "threshold bleeding," allows suppliers to:
Maximize the percentage of rice classified as head rice
Increase profits by selling what would objectively be broken rice at premium prices
Technically remain compliant with ISO standards while subverting their intent
Real-World Implications
This paradox affects various stakeholders throughout the rice value chain:
• Consumers experience inconsistent product quality as batches contain more technically compliant but functionally broken kernels, leading to unpredictable cooking results and texture variations.
• Millers and processors face pressure to engage in threshold bleeding to remain competitive, creating ethical dilemmas for businesses committed to quality integrity.
• Regulators struggle with standards that enable technical compliance while undermining quality objectives, challenging their ability to maintain meaningful oversight.
• Premium producers find their market position eroded by competitors exploiting measurement loopholes, diminishing the value of authentic quality investments.
• Supply chain transparency suffers as manipulation becomes normalized industry practice, reducing trust and complicating quality verification.
Conclusion
The Quality Standard Paradox in rice grading illustrates how well-intentioned standards can create unexpected consequences. By recognizing and addressing this paradox, industry stakeholders can develop more effective quality metrics that align economic incentives with genuine quality improvement rather than statistical manipulation.
As global food systems become increasingly complex, we must ensure that our quality standards evolve to close loopholes and genuinely serve their intended purpose—providing consumers with consistent, high-quality products and creating fair market conditions for producers.
Note: This article reflects personal observations from my professional experience in the industry and is intended to spark discussion on improving quality standards. It does not represent official positions or critiques of specific organizations or standards bodies.
Ron Hadar, Vibe Imaging Analytics
Comments